Effective Quality Maintenance-Relentlessly Developing Rules Based on Understanding of Medical Practices
Doctors use medical equipment to assist them while they are performing medical procedures. Ultra high quality is essential as these devices come into direct physical contact with patients and are used in both diagnosis and treatment.
Manufacturing errors are unacceptable, and workers must be provided with clear instructions. They also need to remain properly focused so that they can carry out these instructions reliably. This is the basis of quality, and Olympus never stops working to ensure that these principles are implemented consistently, both by improving the processes of the systems in our workplace, and also by working steadily to build the proper mental attitudes through training activities.
Perception Gap between Workers and Authors of Work Standards
Tasks should be performed in the prescribed manner. Although this may seem obvious, the fact is that it is not easy to observe every detailed rule while carrying out a task.
We formerly conducted an internal quality investigation. As a result of the investigation, we discovered that the quality defects were due to inadequate supervision in day-to-day operations. To ensure that operations would be carried out more reliably, meetings of all team leaders were called at the Hinode Plant in Tokyo to discuss the issue. This led to a shared awareness of the need to build a corporate culture and structure that would ensure reliable performance of assigned tasks.
When we analyzed the causes of defects in situations where workers were not observing the Work Standards, we found that there was a perception gap between workers and the authors of the Work Standards. The authors had written the Work Standards without sufficient thought about whether the content was sufficiently clear so as to be understood by the workers without being confused. Meanwhile, workers were deciding what was acceptable even though they lacked sufficient knowledge and skills needed to understand and implement their work instructions. If there is cooperation between the workers and the authors of the Work Standards, we could achieve our quality targets. However, un-fortunately there was a gap. And that was the source of our quality defect. In addition, there was another problem that we had systems that were insufficient to allow us to monitor (discover) this gap.
We therefore decided to amend the Work Standards to make them more comprehensible to workers, and to review our employee education policies so that workers would be able to acquire the necessary knowledge and skills. We also decided to strengthen our supervisory systems to allow real-time monitoring of events as they happen.
Analysis "Why do problems with quality occur?"
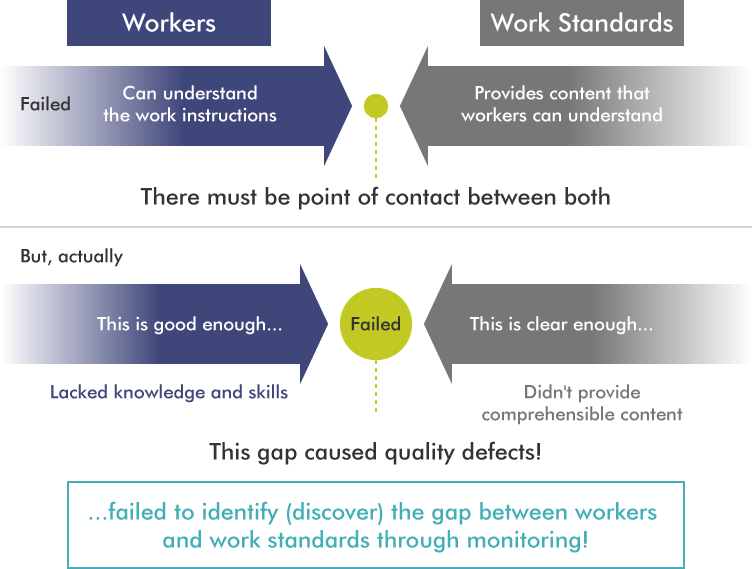
- 1: Amendment of the Work Standards
We started out with the presumption that if a Work Standard required careful thought or caused confusion, it was not enough. Based on this premise, we amended the com-position, format, instructions, expressions, and layout used by setting editorial guide-lines. We also made the standards more easily accessible by distributing them in electronic form.
- 2: Review of Education System
We introduced a licensing system under which workers were required to obtain a license before being allowed to start work. After attending a lecture course and practical training, the workers took written and practical tests. Only those who scored 100% were granted licenses. Each worker repeated this cycle until he or she reached 100%. We also clarified competency requirements by adopting a standard covering educational record-keeping and decisions about fitness for work.
- 3: Improvement of Supervisory Systems
We introduced a daily supervision system, under which supervision was literally carried out every day. The purpose of this system was to ensure that work was being performed according to the Work Standards.
Licensing: the Key to Safety and Confidence for Medical Professionals and Patients
The most important of these three measures was the introduction of the licensing system. We established two license levels: basic and specialist. A worker is eligible to receive a basic license after he or she has completed training and been confirmed as having acquired basic knowledge and awareness by passing a written test. Specialist licenses are granted to those who have attended lectures analyzing detailed elements of process work and pass written and practical tests. Workers are not allowed to start work until they have passed the tests at each level.
The licensing system was applied not only to our regular employees, but also to part-time and temporary personnel. Everyone was determined to pass, and many workers even used their breaks and commuting times to study. Some workers were on the brink of giving up because of the difficulty of the process. However, they all recognized the necessity of the licensing system when we explained to them on an individual basis about the serious responsibilities borne by those who make medical equipment. Eventually everyone passed.
The implementation of these measures resulted in the creation of a structure that ensured the proper work. By providing increased opportunities for communication, it also helped to change attitudes and improve the corporate culture.
Chilling Reminders Provided by Simulation Tests
A similar licensing system has been introduced at Aizu Olympus.
They have also adopted a unique training program based on simulations of quality-related defects. The aim of the program is to provide workers with a simulated experience of the actual consequences of quality defect. By viewing video recordings of news items and reading newspaper accounts of quality defects involving medical equipment, they gained a first-hand awareness of situations that could affect them personally. They also studied examples of defects in Olympus products. Then they studied an actual case of a medical accident (unrelated to Olympus products) in which a medical procedure was performed on the wrong patient. By viewing video recordings of news items and reading newspaper accounts of quality defects in medical equipment, they gained a first-hand awareness of situations that could affect them personally. Then they studied an actual case of a medical accident (unrelated to Olympus products) in which a medical procedure was performed on the wrong patient.

Daily supervision-Two supervisors and a worker study a Work Standard.
These programs have encouraged workers to think about facets of their day-to-day activities in which particular care is needed in order to prevent quality defects. They have also led to group discussions. One participant in these discussion said that he had become keenly aware of the importance of quality, and of the momentous responsibility that comes with making medical equipment, since a moment’s carelessness could cause a problem having the potential to endanger human life. Another said that the programs had provided a reminder of the high risk of errors when work instructions are provided verbally, and of the need to study and understand the Work Standards before starting work. These comments indicate that the training programs have been effective in raising the awareness of workers.
In recent years, similar programs have been implemented not only by medical equipment manufacturers, but also by companies in the transportation sector, including railroad operators and airlines, whose staff are responsible for the safety of countless people. Some companies have established dedicated facilities where they provide training based on case studies of actual accidents.
Quality defects with medical equipment can have extremely devastating implications. We are constantly working to improve quality through a range of initiatives designed to strengthen our systems and remain properly focused. These continued efforts lead to patient safety and customer confidence, and to respect for the Olympus brand.
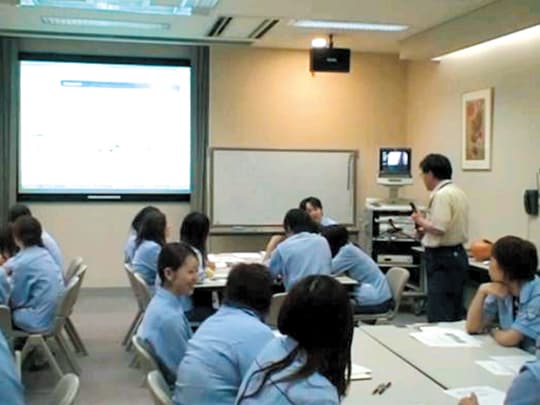
Quality-Related Accident Simulation Training (Lectures using products)